Co2 Casting
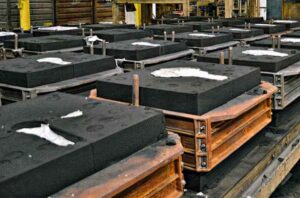
Macraft manufactures CO2 casting, also known as sodium silicate or silicate casting, is a sand casting process that uses a sodium silicate binder and carbon dioxide gas to harden the mold or core. This method is known for its simplicity and ability to produce strong, dimensionally stable molds quickly. Here’s an overview of the CO2 casting process
Applications
CO2 casting is commonly used in the manufacturing of ferrous and non-ferrous metal castings. It is particularly popular for producing large and complex parts, such as engine blocks, pump housings, and various automotive and machinery components.
Advantages
- Good dimensional accuracy: The method produces strong, dimensionally stable molds, resulting in accurate castings.
- Versatility: Suitable for a wide range of metals and complex shapes.
- Cost-effective: Lower cost compared to some other casting methods, especially for short production runs.
No Bake Casting
Macraft manufactures No-bake casting, also known as air-set casting, is a sand casting process that uses a chemical binder to bond the sand grains together without the need for baking or heating. This method is widely used for producing large, complex, or high-precision metal castings
Applications
No-bake casting is commonly used in the production of large, complex, or high-precision castings, such as engine blocks, pump housings, gearboxes, and other heavy machinery components. It is suitable for both ferrous and non-ferrous metals.
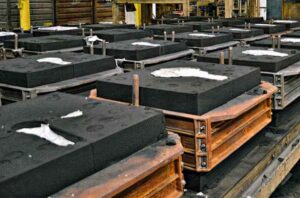
Advantages
- No need for baking/heating: The room-temperature curing process simplifies the operation and reduces energy consumption.
- Versatility: Can be used with a wide range of metals and casting sizes, from small to very large components.
- Excellent surface finish and detail: The use of chemical binders allows for precise and smooth mold surfaces.
- High dimensional accuracy: The molds are stable and do not change shape during the curing process.
Green Sand Casting
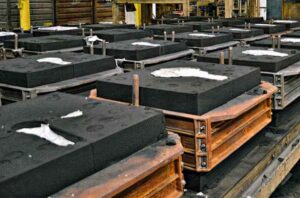
Macraft manufactures Green sand casting its a widely used and cost-effective method of metal casting, utilizing a mold made from a mixture of sand, water, and clay (usually bentonite). The term “green” refers to the fact that the sand mold is not dried or baked, but remains in a “green” or uncured state. This process is popular for its versatility and ease of use
Applications
CO2 casting is commonly used in the manufacturing of ferrous and non-ferrous metal castings. It is particularly popular for producing large and complex parts, such as engine blocks, pump housings, and various automotive and machinery components.
Advantages
- Good dimensional accuracy: The method produces strong, dimensionally stable molds, resulting in accurate castings.
- Versatility: Suitable for a wide range of metals and complex shapes.
- Cost-effective: Lower cost compared to some other casting methods, especially for short production runs.